Denise's coaching cycle with Joe.
- Tilo Schwarz
- Jan 1, 2018
- 7 min read
Updated: May 29, 2023
After her little self-pat on the back, Denise got up and made her way to meet Joe for their first coaching cycle today. Joe was still working on the issue with the damaged seals, and Denise was eager to find out what he had learned from his last step. She had realized how exciting it was to learn along with her improvers.
When Joe arrived at the storyboard, they started their coaching cycle. Discussing the target condition and the current condition went quickly. Then Joe quickly reviewed the actions he had taken and his expectations.
Then Denise asked, "Joe, what did you learn from taking the last step?”
Joe replied, "I observed the following. When screwing in the first screw, the lid often slightly moves because it has some play. This will move the seal with it, and sometimes the seal will slip over hole three on the other side. If this happens, the third screw damages the seal when screwed in. So the problem is not caused at screwing position three, as I initially thought. That is where the damage occurs. The problem is already caused at the first screw when the moving lid pulls the seal along. I guess that is what you refer to as the point of cause.
Denise thought about the Kata Cycle, at what stage are we in our conversation? At 2 o'clock, she realized. The effect and cause of the obstacle are now known. Time to move on to the next step, a type 3 experiment, to find and test a solution to remove the obstacle. Still, Denise hesitated to ask question 4: 'what is therefore your next step?' It seemed to her that this would be too quick. She remembered similar situations in her previous coaching cycles. Often at that point, Mark and Joe had responded with a solution that was difficult to execute, took too long to implement, or was too expensive.
Since Denise couldn’t think of any other approach, she went ahead anyway and asked for the next step.
Joe replied, "I'll talk to the engineering department to see if the play in the lid can be reduced by changing the housing design or if there is a way the seal can be fixed to the housing. Maybe with a little pin on the housing and a fixing hole in the lid.“
Oh no, Denise thought, just as I feared. Both ideas might solve the problem, but will need design changes which will take a long time and be costly, or might even not be possible.
She felt trapped and continued, "Joe, what other options do you see to solve this problem?“ As the words left her mouth, Denise realized that she was no longer coaching.
Joe’s face tightened, and he answered impatiently: "I am out of ideas. We have been working on this obstacle for so long. We have to do something.”
This was getting very difficult. Denise tried to row back, "I understand, but a design change to the lid or seal will not be a quick solution.“
Suddenly, she remembered one of the first tips she had written in her notebook: If it gets difficult for the coach in one phase of the coaching cycle, the problem often originates in the previous phase. Right now, we are in phase 4 (next step), maybe we should move back to phase 3 (obstacle, effect, and cause).
Denise decided to try that and to see what happened.
"Joe, I realize that I'm not helping you right now. Let me try again to find a better way to coach. What exactly happens in the process when the problem occurs?"
Joe replied, "when tightening screw one, sometimes the lid is moved because it has play relative to the housing. The seal then moves with it and, in the worst-case, covers hole three. Then, when the screw is inserted in hole three, it damages the seal."
"Let's sketch that sequence," Denise suggested.

While Joe did so, Denise noticed that he had mentioned two variables. The lid only shifted occasionally. Furthermore, the seal did not always end up in an unfavorable position over hole three, even if it was pulled along by the lid. Joe probably had not yet realized that for himself.
When Joe was finished writing down the steps, Denise picked up on her thoughts. She asked, "what exactly happens in the process for the lid to shift sometimes and not others?"
Joe replied, "that depends on how it is positioned in the housing. If it touches the right edge, it does not move. If it is positioned touching the left inside edge of the housing, it has some play. Therefore, it will be moved to the right when screw number one is tightened.“
Denise probed on her second observation. "And what exactly happens in the process for the seal to cover hole three when it is pulled along?“
Joe explained, "that depends on how the seal is positioned on the housing. If it is aligned with the left side of the housing, it is simply moved along and ends up in the correct position. However, if the seal is placed too far to the right, the lid pulls the seal beyond hole 3.“
"Let's add the steps for inserting the seal and lid to our sketch of the assembly sequence," Denise replied. She pointed to the sheet on which Mark had written down the process steps.
After Mark had added the two steps, Denise continued investigating. "And what should be happening, so the process runs correctly?”
Joe went through the sequence step by step, explaining: "The seal should be positioned, so it can't move over hole 3 even if it is pulled along. To do so, the seal should be aligned with the left inside edge of the housing. Likewise, the lid should be placed touching the right inside edge of the housing, minimizing play so that it will not move when the first screw is tightened. But this will be difficult for the team to assemble as they have to do two different positioning steps."
Denise responded quickly, “that is a great explanation, Joe. You have an excellent grasp of the process. What other options do you see to get the process to work correctly?”
Joe thought about it some more, "Perhaps we could change the order of the assembly steps and put the seal on the lid instead of placing it on the housing. This will align the seal exactly with the lid. Then we insert the lid together with the seal into the housing and make sure the lid touches the right inside edge of the housing, thus reducing the play. That way, the lid can't move, and the seal is aligned with the holes in the lid."
Wow, now we’re getting some place, Denise thought. She asked Joe to sketch the desired sequence as well.
"But I am not sure if that really works," Joe noted while doing so.
Denise was really getting excited. Now we have reached his threshold of knowledge.
She replied, "Don't worry if you don't know, what is therefore your next step to finding out?“
"I'm can run some assembly tests with the new sequence and see what happens," Joe replied.
"And what do you expect then," Denise asked further.
"I don’t know, mind you, but I hope that the seal will not slip over hole three when screw one is tightened. And therefore, there will be no damaged seals," Joe replied.
Denise and Joe completed their coaching cycle by writing Joe's next step and expectation into the experimenting record. Then they agreed to meet again on Monday at 9:00 am.
That was quite different now, Denise thought as she walked back to her office. As she reflected on her coaching cycle she realized something interesting. After she had asked question 4 (next step) too fast, Joe had proposed a premature solution. Moving back to phase 3 by asking, "what exactly happens in the process for the problem to occur" had really helped. Joe had described the relevant sequence much more precisely.
Afterward, the question ‘what should be happening so the process runs correctly?, had shifted his perspective. All of a sudden, the two options 'aligning lid' and 'aligning seal' had leapt out.
Denise wrote down the two useful questions in her notebook.
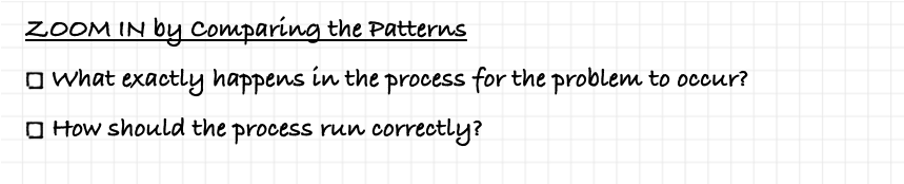
With the first question, the coach can help the improver investigate more deeply the current state of the process that caused the obstacle, Denise thought. Today it helped us to understand that the lid moves when placed touching the left side. And that the seal moves with it and covers hole three when placed to the right side.
The second question produced a desired pattern for the process that we could compare with the existing pattern. Lid doesn't move when placed touching the right side. If the seal is positioned on the left side, even if it is pulled along, it does not move far enough to slip over hole 3.
Although this seemed only marginally different from the design solutions Joe had proposed to reduce play of the lid and/or hold the seal in place, the difference in perspective was important and freed up Mark to think more broadly of options.
Perspective 1: Reduce play between lid and housing and keep the seal from moving.
There probably was only one possible solution, a change in design to achieve this.
Perspective 2: Keep lid from moving and align seal with lid and holes.
For perspective 2, several options became possible, Denise realized. Aligning the lid with the right side of the housing was one. Alternatively, placing two opposing screws into the holes before tightening them was a second. Likewise for the seal. Align lid with the left inside of the housing instead, so it doesn't matter even if it moves.
This change in perspective had somehow sparked new ideas from Joe. He had realized that positioning the lid touching the right side would keep it from moving. Then it was only necessary to have the seal aligned with it rather than keeping the seal from moving as well. That was a lot easier to achieve.
Opposing the current process pattern with the desired process pattern seems to open the solution space, Denise thought and called her new trick "Compare the Patterns.“
That was somehow counter-intuitive. If a solution was not working, asking for an alternate solution was a dead-end road. If in need of alternative ideas, it was a lot better to go back and dig deeper into the current condition and the obstacle .